California engineer Curtis Wong is applying tech innovation to the affordable housing crisis and hoping his ideas will take hold across the U.S.
The former employee of Elon Musk’s SpaceX is the founder of startup Cloud Apartments, which has a patented design for contemporary, cool-looking apartment modules and snap-together construction. The young company, based in San Francisco’s Bay Area, has received state approvals and they are working on a San Jose, Calif., site to erect a six-storey, 205-unit apartment building over a concrete podium, made up of “tech’d out” studios and one- and two-bedroom units. He has four other deals underway with developers, totalling 1,000 units in the Bay Area. Because off-site, factory-built modular construction is generally much faster than conventional on-site construction, he says the units will be more affordable due to savings of around 30 per cent.
Mr. Wong says it’s going to take a more creative approach that defies the norm if North Americans are going to solve the affordable housing problem. He had worked as a structural engineer for several years but grew tired of the lack of innovation, so he joined space exploration company SpaceX and worked on the launch pad in Cape Canaveral, Fla. The work pace was thrilling but too exhausting, so he went back to school and obtained a masters of business administration degree from Harvard University. He quickly discovered he could apply his tech know-how to housing, by standardizing the process.
“There are reasons that innovation is so hard within construction compared to SpaceX, if you want to compare those two worlds,” Mr. Wong says. “With SpaceX, there are no regulatory government agencies watching you the whole time, making sure you are following building codes. You cowboy it, do what you want and a lot of cool stuff happens. Within construction there are lenders, developers, government agencies permitting all that stuff, and it slows you down from innovating. … What I know about innovation, and bringing that back to the construction industry was pretty tempting.”
The goal is to wipe out the negative image of modular construction, the way that the electric car went from being an outlandish idea to today’s Tesla. The unique angle on construction is that the high-tech units are shipped to site 95-per-cent complete, a “plug and play” approach to building. Cloud’s studio apartment has built-in moveable furniture, such as bed that lifts up to make way for a couch, a projector for TV watching and an integrated battery that can power the unit off the grid for 24 hours. Such features are useful in the face of climate change.
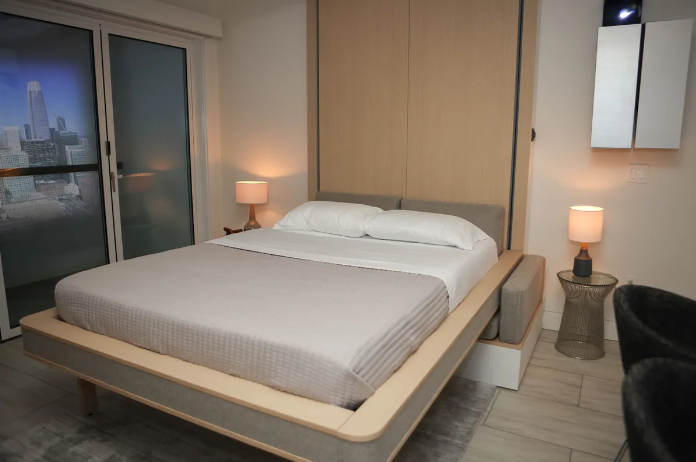
But the key to his concept is not just designing cool interiors, but standardization of the units. He says they can reduce construction time by 50 per cent, and with their team of collaborators, they have the capacity to build about 10,000 units a year.
A standardized building design would also expedite permitting times because developers wouldn’t have to start all over again as they do with a one-off design.
“If you want to talk about how to use modular to save on costs, you have to think about it like how you think about automotives,” Mr. Wong says. “Henry Ford reduced the cost to build a car based on the assembly line that he pushed. The way he did that, he had the assembly line, mass efficiency through the factory, and standardization of what the automobile is – you paint them all black, you churn them out make them accessible to mainstream America and the world.
“What we are doing with Cloud Apartments is using the same mindset with modular, because currently modular is not standardized. Every building is still a one off, and totally different.
“We are completely standardizing the units by thinking of them like products.”
The hotel industry has already cottoned on, with major hotel brands such as Marriott now building modular construction. The chain just built the world’s tallest modular hotel in New York with pre-fabricated and pre-furnished guest rooms, a 26-storey building topped off with a modular rooftop bar.
“Building in a factory is how luxury cars are made, so the potential is much higher to make a nicer quality [home]. There are a ton of efficiencies, not just the improved quality, but also driving down the cost of housing.”
His company works with local factories and furniture designers. The units are state-approved, although they would still have to be approved at the local level.
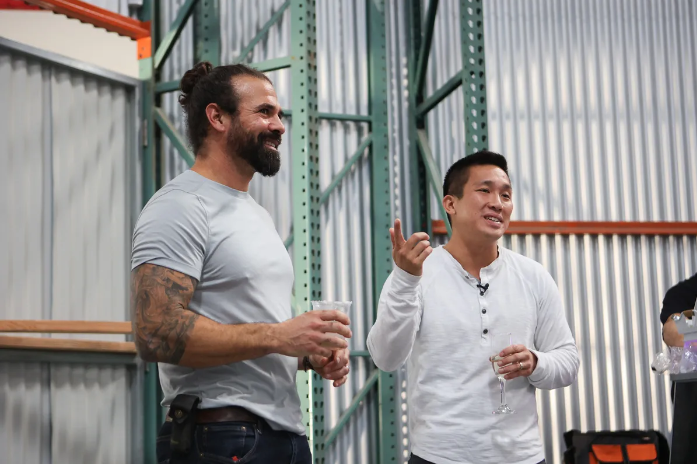
“Out here, we have state of California permits for factory built housing. We did that whole process so that the Cloud-S unit can be built anywhere in California now. It’s one little advantage of modular construction, at least in state of California, that you have a better approval process.”
Part of the reason that the industry is starting to look to off-site construction is for the same reasons that European countries and Japan embraced the method: to reduce energy costs. The labour shortage is another.
According to BuildForce Canada, the residential construction sector will need 107,000 new workers over the next decade. And that number doesn’t even factor in federal initiatives to double the number of new homes built over the next decade, to address record-setting immigration.
“The idea of importing highly skilled tech workers is great, but where are they all going to live?” asks Rocky Sethi, chief operating officer for Adera Developments.
Adera is one of several Vancouver area developers that have embraced the use of off-site construction. This year the company launched two projects built with its patented mass timber sound absorbing panel system, Pura in Surrey, B.C., and SoL in West Coquitlam, B.C. Mr. Sethi says prefabricated off-site methods used for their Crest condo development in North Vancouver, B.C., resulted in a labour reduction of about 50 per cent. The building was framed 30-per-cent faster than usual, says Mr. Sethi. That’s helpful, because the number of tradespeople is in rapid decline, due to the fact that they’re aging out and the younger generation isn’t going into the trades.
“I’ve been in construction for over 20 years and the funny thing is we always talk about a shortage of labour. Skilled labour has always been a challenge but now it’s a challenge getting labour of any kind. And it’s not just through peak periods,” he adds. “We don’t have enough people to sustain us through a somewhat slower market over the next six to 12 months.”
But the challenge to using modular is the many municipal regulations that get in the way and don’t necessarily add anything to the project, Mr. Sethi says.
“What the industry needs to focus on is delivery of housing. Otherwise, it just makes my development more expensive and takes more time for approval. [For example], re-orientating a building, how does that make one bit of difference to somebody who needs a home to live in? It doesn’t.
“I think that modular does have a place, but we have a long way to go until that’s widely adopted for a number of reasons way outside the control of modular home builders. We are talking provincial and municipal rules and regulations, and we have 22 municipalities in Metro Vancouver that all have their own requirements.”
The innovative construction business is not without its risks. Mr. Wong worked on Starcity Minna, a 16-storey, 270-unit residential modular high-rise targeting middle-income residents that was also started by a tech entrepreneur. Plans for the project fell apart during the pandemic. But despite pushback, it had reached the approval stage. Mr. Wong sees that experience as a learning opportunity.
“That was somewhat of a bomb when the planning commission in San Francisco saw we wanted to do modular. It’s probably the same in Vancouver and everywhere, ‘oh it’s low-quality housing, we don’t want it.’ But one thing that is starting to change is that reaction is disappearing from other cities that have done modular.”
Craig Mitchell, principal of Vancouver-based BlackBox Offsite Solutions and modular construction expert, says he’s been tracking U.S. companies such as Cloud Apartments because they are moving into market-rate rental. In Canada, the modular industry has seen growth because of government-funded social housing.
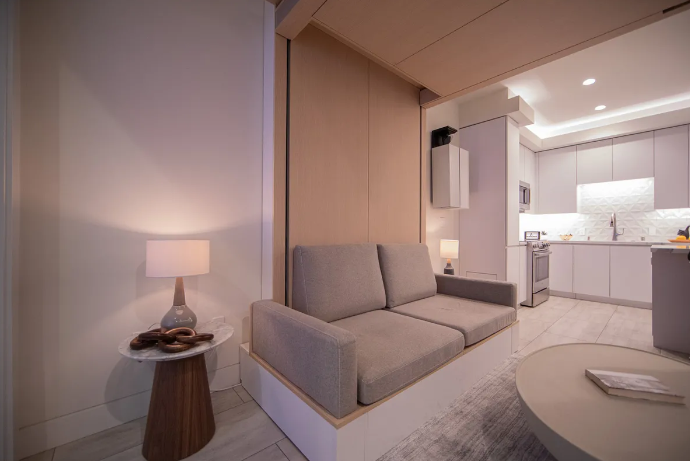
Mr. Mitchell said there is considerable interest among private U.S. developers to use off-site construction.
“It’s the private developers and owners that have now adopted modular as they are seeing great case studies, which his attracting considerable investment,” he says of the U.S. market.
“The development costs with conventional construction are astronomical, so they are beginning to accept alternate forms of construction more readily, which are bringing new players into the market.”
It helps that the U.S. has denser markets than Canada, he added.